關於量測誤差
在此說明量測誤差的原因及其消除方法。
何謂量測誤差
在某種因素的影響下,量測結果不同於應當得到的量測結果(量測值)時,稱為「量測誤差」。
量測誤差的原因各不相同,必須依據原因採取相應的處置措施。發生量測誤差時,十分重要的一點是在充分探討「為何會產生量測誤差」的基礎上採取應對措施,實現製造產品的品質穩定。
量測誤差的原因
量測誤差可分為3種模式,分別是測量儀導致的量測誤差、量測人員導致的量測誤差以及環境條件和目標物導致的量測誤差。各模式中的代表性原因匯總如下。
量測誤差的種類 | 量測誤差的原因 |
---|---|
測量儀導致的量測誤差 |
|
量測人員導致的量測誤差 |
|
環境條件和目標物導致的量測誤差 |
|
測量儀導致的量測誤差的消除方法
不僅使用的測量儀規格必須與量測用途相符,有時也可藉由安裝和使用方法消除誤差。另外,還列舉了經年使用導致的消耗品老化等引起的量測精度降低所導致的量測誤差的消除方法。
以參考距離量測從而提高重複精度
三角測距方式(三角測量方式/三角測定方式)的位移計中,目標物的位置不同,重複精度會發生變化。如下圖所示,目標物越接近參考距離,光點直徑越接近集中狀態,重複精度提高。難以改變量測距離時,透過選擇和使用配備符合參考距離的光學系統的測量儀,可以減少量測誤差。
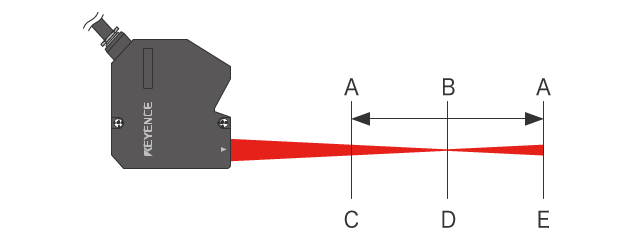
- A
- 不佳
- B
- 良好
- C
- 近側
- D
- 參考距離
- E
- 遠側
但是,雷射位移計中的重複精度有別於量測精度。重複精度是指在“工件和感測頭都靜止的狀態下的量測值偏差”。換言之,即反覆移動同一物體,在完全相同的點量測時的量測值偏差量。但是,雷射位移計在目標物的表面粗糙度和反射率的影響下會產生誤差(詳細內容和對策請參照下文),在相同的條件下量測完全相同的點並不現實。
並且,目標物的表面狀態會導致產生何種程度的誤差,取決於鏡頭等光學設計以及量測演算法(實際輸出值不同),體現為雷射位移計的性能帶來的價格差異、鏡頭大小導致的感測頭尺寸差異等。
藉由修改治具和濾波器實現的微振動對策
改善重複精度後仍存在量測值偏差時,原因可能是安裝治具的振動。位移計的量測方向非水平方向時,若是人員出入的場所,必然會產生垂直方向上的微振動。這種微振動會導致量測值出現0.1 μm至數μm的偏差,對此有效的對策如下。
- 使用低通濾波器功能(或使用搭載低通濾波器的位移計)
- 使用一體化治具固定感測器和工件。
藉由直線性改善實現的對策
玻璃和鏡面等入射角與反射角相同的工件,為了避免鏡面反射導致的錯誤,會將感測頭傾斜。此時,透過減少安裝角度偏差導致的直線性惡化,可以糾正量測誤差。
安裝時必須慎重考量,例如抵住突出銷並用螺絲固定感測頭等。另外,透過盡可能縮小量程,在該範圍內使用基準工件(作為基準的工件)進行跨度調整,也可以改善直線性。
但是,大部分情況下測量儀本身的直線性取決於光學系統,因此即使採取添加移動平均等濾波器的措施也並無效果。如果是鏡面反射安裝狀態且規格中未標明直線性的感測頭,直線性可能出現超出預期的惡化,因此需要注意。

- A
- 突出銷
實施定期校正(校準)
定期校正(校準)是維持測量儀精度不可缺少的作業。以適當的間隔實施校正和維護,可以阻斷量測誤差的根本原因。校正間隔依據測量儀的結構、零件的消耗和老化速度等而有所不同,因此一般來說測量儀廠商會有建議校正間隔,遵守該間隔十分重要。在嚴酷環境下使用,或是受到強烈衝擊等,導致量測誤差無法改善時,需要進行維護或修理。此時,無論是否到達校正時間,都建議諮詢廠商。
量測人員導致的量測誤差的消除方法
離線使用游標卡尺和測微計等測量儀時,不同量測人員的量測位置存在偏差,經驗和技能也存在差異,都可能導致量測結果產生誤差。必須徹底實施教育和培訓,盡可能減少偏差,但無法將量測值完全定量化。另外,目標物存在較小的毛邊或缺口、或是接觸到灰塵附著處進行量測時,量測值會產生誤差,因此必須仔細對量測位置的狀態進行目視確認。並且,無法以資料方式即時掌握量測值,因此檢查與製造同時進行時,可能出現良率降低,無法依據統計資料判斷何時開始出現不合格品等。
而投影機、工具顯微鏡、CNC影像尺寸測量儀、三次元測量儀等量測設備,不但存在量測人員導致的誤差,還必須具備專業知識。為了解決量測業務的人為因素影響等問題,必須徹底實施教育和訓練,長期培養量測人員。
消除離線量測中的量測誤差的測量儀
KEYENCE為了解決這些問題,開發出了只需將目標物放置於載物台上並按下按鈕,即可對多個目標物的多處位置批量實施高精度量測的影像尺寸測量儀。自動補正工件位置和方向,因此不需要定位、方向對齊以及原點復歸等作業。
不要求量測人員的經驗、技術和知識,可在短時間內對更多目標物實施無偏差的定量量測。量測結果全部資料化,因此可透過網路遠隔即時掌握檢查結果,實現資料分析作業的效率化。
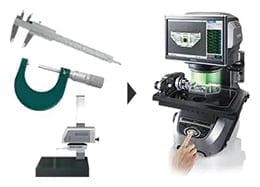
環境條件和目標物導致的量測誤差的消除方法
說明電源接通後的時間、環境溫度與位移計的溫度特性的關係、目標物的材質等導致的量測誤差的原因及其消除方法。
掌握溫度變和飄移導致的誤差
透過掌握各部分的溫度導致的飄移,可以消除量測誤差。量測系統整體的飄移,可以分為位移計單體的飄移成分和治具單體的飄移成分。其中位移計單體的飄移成分有初始飄移、溫度飄移和經時變化。在此解說容易依據規格計算得出的位移計單體的飄移以及由此導致的誤差的掌握方法。
- 初始飄移
- 從電源接通至位移計的內部溫度穩定期間量測值變化的成分。一般在通電後經過30分鐘至1小時,內部溫度和量測值達到穩定。
- 溫度飄移
-
使用環境的環境溫度變化時,量測值變化的量。規格上標示為溫度特性,格式為「〇〇% of F.S./℃」。
例如,如果量測範圍為±5 mm(也即10 mm的範圍)、溫度特性為「0.01% of F.S./℃」,
則環境溫度變化10℃時的溫度飄移,可使用以下公式計算。0.01%(溫度特性)×10 mm(量測範圍)×10℃(環境溫度)=10 μm(溫度飄移)
由此可知,環境溫度變化10℃時,會因位移計的溫度飄移而產生10 μm的量測誤差。
使用類比訊號從感測頭向控制器傳送時,還應考慮到控制器的溫度飄移,依據控制器的溫度特性規格以同樣的方式計算。使用現在位移計中主流的數位訊號傳送時,也可以使用上述公式。
並且,若是知道感測頭筐體內的溫度會有何種程度的上升,依據初始飄移的參考溫度飄移進行計算,即使接通電源後立即使用也可以將其納入考量實施量測。其計算方法如下:
內部溫度上升(T℃)×溫度特性(〇〇% of F.S./℃)×量測範圍(mm)
- 經時變化
-
位移計單體的經時變化,其產生原因是固定光學系統的黏著劑在細微的溫度變化下發生膨脹、收縮等。經時變化也依感測頭的不同而存在不同的溫度特性,飄移的方向也存在個體差異。一般來說,位移計的溫度特性越小,越具備穩固的結構,經時變化也越小。
其他還有治具、固定螺絲等也會產生飄移。要求高精度時,可以根據治具材質的膨脹係數、膨脹方向以及固定螺絲的殘留應力等計算飄移導致的誤差,但因素越複雜,越難以計算實際產生的量測誤差。
目標物的表面狀態導致的誤差和偏差的應對方法
即使是高精度的雷射位移計,有時也會受到目標物表面狀態的影響。這一因為對工件的依賴性高。這是發生量測誤差的原因中最常見的一種,但僅僅查看規格或型錄,無法瞭解會產生何等程度的偏差。
目標物表面狀態的影響導致的誤差,可以分為3種,即顏色偏移成分、表面凹凸的影響導致的誤差成分、表面的反射率變化。
這裡將說明其中具有代表性的誤差產生原因,目標物表面凹凸的影響的對策和消除方法。以下3種對策可以減少表面的凹凸程度導致的影響。
- 盡可能減少目標物的凹凸
- 如果是研磨等表面處理製程,則在製程後而非製程前量測,有表面光滑的面時則從該側進行量測等,由此或許可以消除誤差。另外,如果可實現,研磨表面減少凹凸、粘貼陶瓷等也是有效的方法,但若只為了量測而增加製程,並無可實現性。
- 使用濾波器功能
-
使用移動平均、低通濾波器、中值濾波器等,減少量測資料的偏差。目標物移動時,使用移動平均的濾波器處理,可以減少表面狀態帶來的影響。
例如,假設在搬運中對高度1 mm左右且有凹凸的工件進行量測時,量測值存在偏差。透過計算出工件移動中多次量測的平均值的移動平均濾波器處理,可以實現量測值的穩定。但是,若是濾波器使用過多,則會無法反映原本的波形,因此需要注意濾波器的設定。例:清潔刮刀的彎曲量測 無移動平均濾波器處理 實施移動平均處理後資料穩定 並且,量測不同位置的表面狀態不同的金屬髮絲紋等目標物時,雷射光照射到不同部位時的方式不同,因此移動目標物並將表面狀態不同的多個位置的量測值平均化,可以減少量測值的偏差。
- 加寬發射的雷射光和受光元件
-
發射比小光點雷射光更寬的光束,可以減少凹凸導致的數值偏差。使用投光鏡頭上搭載特殊形狀的圓柱狀鏡頭的位移計,可以發射僅橫向寬度加寬的線性雷射光束。
並且,透過採用加寬的受光元件(CMOS和CCD)可以直接接收加寬後的全部反射光,因此可以吸收雜亂光導致的接收位置偏差。
需要高精度量測大範圍的細微凹凸形狀時,使用發射帶狀狹縫雷射光的高精細雷射位移計,可以高速且正確、無誤差地量測2D輪廓資料和3D形狀。
例:印刷電路板網版印刷厚度量測 2D輪廓資料 3D影像處理