即時量測和分析變形印刷電路板的精確 3D 形狀的方法
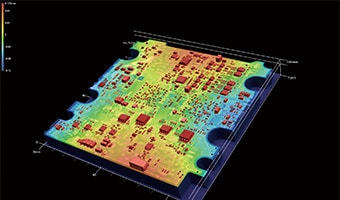
在安裝電子元件和設備的回流焊製程中,印刷電路板會因焊膏(焊膏)和粘合劑的結合以及加熱而受到應力。回流焊製程實現了高效的元件安裝,但加熱產生的應力會導致印刷電路板翹曲、起伏和變形等熱變形。如果印刷電路板變形,零件的結合強度和與外殼的貼合度都會下降,這將大大影響良率。
在這裡,我們將解釋從印刷電路板變形的基礎知識到量測變形時的問題以及最新的量測方法。
- 什麼是印刷電路板“變形”?
- 印刷電路板變形的模擬分析與評估
- 使用以往量測設備進行印刷電路板變形量測和評估的問題
- 印刷電路板變形量測中的問題解決方法
- 總結:顯著改進難以精確量測的整個印刷電路板變形,提高量測效率
什麼是印刷電路板“變形”?
印刷電路板(印刷線路板)的表面應平坦以正確安裝元件,但過大的熱應力會導致翹曲、起伏和熱變形。下面列出了印刷電路板變形問題的出現背景及其影響。
印刷電路板熱變形的背景
隨著電子元件貼裝印刷電路板的多層化、小型化和高貼裝密度,開始採用使用回流焊方式的元件貼裝。在回流焊製程中,根據需要在電路板上印刷焊膏(錫膏),然後塗上用於固定零件的粘合劑,然後使用貼片機將電子零件放置在印刷電路板上。通過將其放入爐中並加熱錫焊或硬化結合,可以實現高效的元件貼裝。
在回流焊製程中,隨著考慮環保的無鉛焊錫的引入,現在需要比以前更高的熔化溫度。提高回流焊爐中的溫度會增加印刷電路板上的熱應力。印刷電路板在高溫爐中翹曲、起伏等熱變形的問題增多。
印刷電路板變形的影響
如果印刷電路板變形,可能會由於未對準等原因導致無法正確錫焊,或者應力可能會施加到焊接部分,從而發生連接不良,或在發生較大的變形時,與導致外殼裝配的配合精度降低等故障。這些缺陷會顯著降低良率。
此外,如果產品在組裝到外殼後發貨,而沒有注意到印刷電路板部分或整體輕微變形,則產品可能會因電子元件連接不良而在以後發生故障,從而導致投訴。尤其是汽車和飛機的控制印刷電路板,故障可能導致事故,所以印刷電路板的形狀與導線翹起或者焊錫圓角的形狀一樣可以說是一個重要的檢查項目。
印刷電路板變形的模擬分析與評估
為抑制印刷電路板變形的改進需要在實際加熱後的設計和評估等各個階段對加熱條件進行研究、驗證和評估。
使用軟件進行變形模擬分析
在印刷電路板設計階段,我們有時會使用 CAD 數據進行模擬分析。用於模擬和評估物體變形行為的方法之一是有限元法(FEM:Finite Method Element)。
什麼是有限元法
有限元法(FEM)是一種模擬分析方法,即使是複雜的形狀也被分割(離散化)為簡單形狀的集合體(元素),首先求出各個簡單形狀的應力和變形。通過將每個簡單結構堆疊到原始整體結構來設想整體每個部分的應力和變形。通過使用對象產品的CAD數據在計算機軟件上執行此操作,可以對剛性、強度、耐振動性、塑性變形、斷裂、熱變形等進行模擬分析。
元素根據其形狀分為以下類型。
0維元素 (標量) |
![]() |
||
---|---|---|---|
一維元素 (條) |
![]() |
||
二維元素 (殼) |
![]() |
![]() |
|
三維元素 (實體) |
![]() |
![]() |
![]() |
- 0維元素(標量):沒有形狀的點。
- 一維元素(條): 線性:用於製作桿、柱、樑等線。
- 二維元素(殼):面。用於薄板材料等。
- 三維元素(實體):表中從左起分別稱為三棱錐四元素、三棱柱五元素、長方體六元素,分別使用這三種。通過使用許多六元素,可以提高厚物體的分析精度,但難度大,需要大量計算時間。另一方面,使用四元素自動創建 三維元素網格的技術先進且計算時間短,因此在時間縮短優先於高精度。
模擬分析的主要特點和流程
維度越低,形狀越少,因此分析處理花費的時間越少,維度越多,越需要更多的時間,但是可獲得精度更高的數據。作為三維元素印刷電路板變形模擬的一般流程,首先將印刷電路板的設計數據劃分為網格狀的元素。大多數印刷電路板設計數據都是 2D 格式,但有些軟件需要將其轉換為 3D CAD 格式。根據回流焊製程中溫度曲線的加熱溫度,虛擬地對每個網格元素施加溫度升高時的應力,並獲取假設數據。
印刷電路板發熱測試及實測/評估要求
需要將經過模擬的印刷電路板實際放入回流焊爐中,驗證和評估假設的溫度曲線是否與模擬的一樣。
雖然取決於尺寸,但據說如果使用有限元法將印刷電路板分成三維元素,元素數可達到約 50,000 個。換句話說,如果不能高精度地量測印刷電路板整個表面的形狀,那麼無論模擬分析多麼精確,都無法獲得正確的驗證結果。實測是一個非常重要的過程,以免忽視設計階段需要改進的地方。
接下來,我們將解釋使用以往量測設備進行量測的挑戰以及可以與使用計算機的高精度模擬進行比較和評估的最新量測方法。
使用以往量測設備進行印刷電路板變形量測和評估的問題
以往的輪廓形狀量測儀、三維量測儀等量測儀難以準確量測整個印刷電路板的形狀,即使進行高度的模擬、試驗和實測也難以對樣本的形狀及其變化進行定量量化和評估。使用以往量測儀的量測存在以下問題。
使用輪廓形狀量測儀進行變形量測/評估的問題
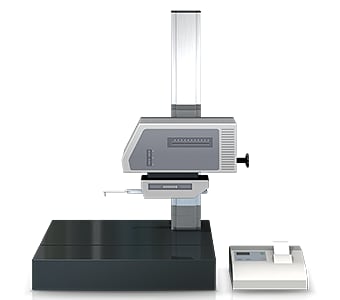
輪廓形狀量測儀是用稱為測針的觸針在對象物表面進行描摹,量測並記錄輪廓形狀的設備。
近年來,也有機型使用雷射代替觸針,通過非接觸式描摹輪廓來應對複雜形狀的量測。一些機型能夠量測頂面和底面。
在使用輪廓形狀量測儀進行印刷電路板變形的量測和評估時,存在以下問題。
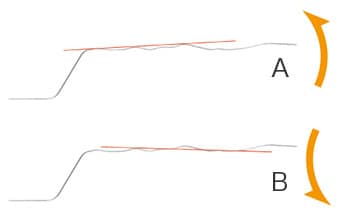
- A
- 向右上升
- B
- 向右下降
- 很難量測和評估大範圍的變形,因為對象物是通過描摹一條線來量測的。
- 無法掌握對象物整個表面的形狀。
- 表面黏著後的印刷電路板等待測面以外的表面有凹凸(貼裝部件)時,印刷電路板本身是否變形則難以量測。
- 由於很難用直線設置參考平面,因此可能會出現量測誤差(圖)。
使用三維量測儀進行變形量測/評估的問題
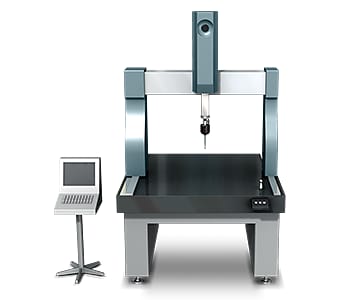
通常,為了用三維量測儀量測印刷電路板的變形,需要將探針尖端的接觸器接觸到待測對象物表面的四個或更多個角上。
例如,對於板構件,通常量測6-8個點。如果量測範圍較寬,增加量測點數可以讓您從更多部位獲得量測值並提高量測精度。
在印刷電路板變形的量測和評估中,存在以下問題。

- A
- 對象物
- B
- 探針
- 不可能獲得整體形狀,因為必須在有限數量的點上進行接觸。
- 量測多個點以獲得更多的量測值需要花費大量時間,並且無法掌握細節形狀,例如整體形狀和凹凸不平的部位。
印刷電路板變形量測中的問題解決方法
由於以往的量測儀是通過線和點來量測的,因此無法掌握整個變形印刷電路板的形狀。此外,很難獲得整個對象物所有凹凸的最大值和最小值,並立即進行定量比較。
為了解決這些量測問題,KEYENCE 開發了表面 3D輪廓量測儀“VR 系列”。
可以以非接觸方式在“表面”準確捕獲對象物的 3D 形狀。此外,可以在最快 1 秒內對量測台上的對象物進行 3D 掃描,以高精度量測 三維形狀。因此,可以在量測結果沒有偏差的情況下瞬時進行定量量測。這裡介紹一些具體的優點。
優點一:最快1秒。以“面”批量獲得整個對象物的3D形狀。
“VR系列”可以在1秒內以非接觸方式一次性在貼裝印刷電路板上獲取80萬個“表面”數據。由於獲取的 3D 形狀的最大和最小的凹凸(高度和深度)可以用彩圖表示,因此可以“可視化”整個對象物的變形部位。
此外,還可以通過直觀的操作在掃描數據上畫出圓弧線、直線、平行線、垂直線等各種輪廓線。可以進行準確的輪廓量測,因此可以快速獲得變形區域的詳細數據。即使在量測之後,也可以根據過去通過 3D 掃描獲得的廣泛數據量測另一部位的輪廓,而無需重新設置對象物。
此外,可以將形狀與設計數據或加熱前的印刷電路板掃描數據進行比較,比較加熱條件不同的多個印刷電路板的量測數據的形狀,並同時將量測項目應用於多個數據。
這不僅可以實現準確的量測、比較和評估,還可以大幅減少工時並提高業務效率。
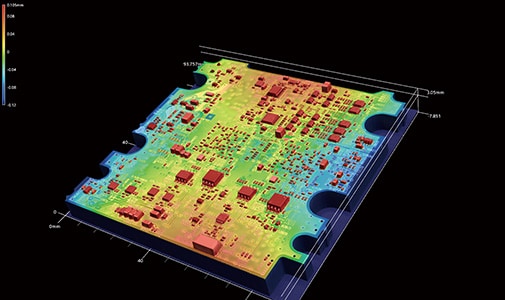
優點二:操作簡單,無論誰量測,量測值都不會出現偏差。
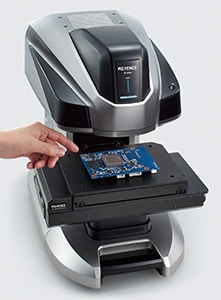
只需將對象物放在量測台上並按下按鈕的簡單操作即可量測 3D 形狀。
通過在低倍率相機和高倍率相機之間切換,即使是小印刷電路板也可以用一台量測儀精確量測印刷電路板的整體或細部。
另外,由於可以根據對象物的特徵數據自動校正位置,不需要進行嚴格的調平和定位。業界首創的“智能量測功能”可以確定對象物的尺寸,自動設置量測範圍,並移動量測台,完全消除了設置量測長度和 Z 範圍的麻煩。
此外,通過使用豐富的輔助工具,您可以直觀地設置所需的量測細節。
除了簡單的設置外,即使是初學者也易於操作,因此即使是不熟悉量測的人也可以在最快 1 秒內進行準確的量測。因此,不僅可以輕鬆實現設計和模擬的驗證實驗和評估,還可以輕鬆實現量產過程中量測和檢查的N增加和趨勢分析。
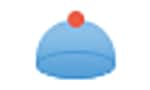
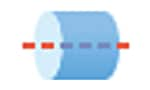
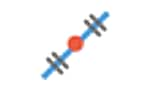
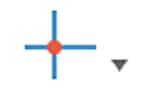
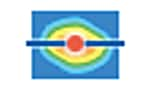
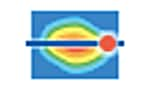

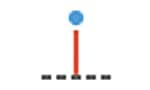
總結:顯著改進難以精確量測的整個印刷電路板變形,提高量測效率
使用“VR 系列”,可通過高速 3D 掃描以非接觸方式即時量測對象物的準確 3D 形狀。除了量測整個印刷電路板的 三維尺寸外,您還可以快速執行以前難以完成的作業,例如量測精細高度和凹凸形狀,以及比較多個數據。
通過引入“VR系列”,您可以解決迄今為止量測中的所有問題。
- 可以使用彩圖可視化整個對象物的高度差異。
- 您可以輕鬆地比較多個量測數據並一次應用所有條件,從而顯著提高工作效率。
- 掃描後,可以量測任何位置的輪廓並比較多個數據。
- 操作簡單,無需定位,只需將對象物放在量測台上,按下按鈕即可。消除對個人量測作業的依賴。
- 由於可以簡單、高速、高精度地量測 3D 形狀,因此可以在短時間內處理大量的 N點。可以幫助您提高品質。
- 消除因人而異的量測值偏差,實現定量量測。
此外,與CAD數據的比較和公差範圍內的分佈也可以很容易地進行分析,因此不僅可以用於研發、設計和測試等階段,還可以用於量產投入後的抽樣檢查、以及不良發生時的原因追查等電子產品製造的各種場景。