解決熱處理後的變形量測問題
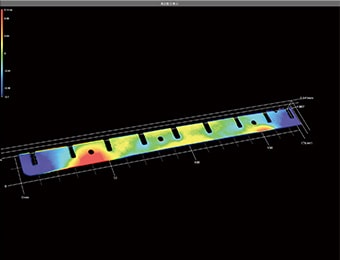
“熱處理”一般是指對材料或產品施加熱量的處理。包括金屬熱處理的材料加工和食品的熱殺菌等,這裡,我們將考慮金屬熱處理引起的變形。熱處理引起的變形在方材和棒材中是收縮和翹曲等簡單的變形,但在形狀複雜的產品中,則變成三維變形,需要先進的技術來量測。
在這裡,我們將講解熱處理變形的基本知識,該熱處理主要用於控製鋼鐵材料的組織和提高其性能,同時講解變形的量測問題及其解決方法。
什麼是金屬熱處理?
金屬熱處理是對金屬材料進行加熱和冷卻以改變其性能而不改變其形狀的加工技術。改變的特性包括強度、硬度、韌性、耐衝擊性、耐磨性、耐腐蝕性、耐蝕性、切削性、冷加工性,分類為諸如切割和塑性加工那樣的金屬加工的一種。
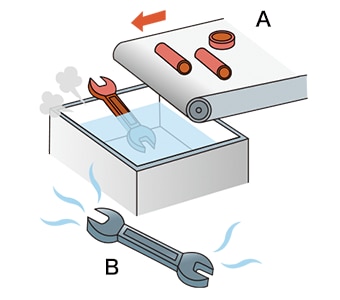
- A
- 變紅(加熱至金屬變紅)
- B
- 冷卻(冷卻至金屬變黑)
熱處理變形例(相變引起的體積變化)
熱處理有“淬火”、“回火”、“退火”、“正火”等加工方法,在這些加工過程中,會發生稱為“相變”的現象。
相變是金屬因熱處理從固態變為液態,反之亦然,由於溫度的變化而引起的晶格和存在形態(組織)的變化。當組織因相變而變化時,體積也發生變化,從而導致變形。
例如,共析鋼(含碳量約0.8%的鋼)從室溫加熱到奧氏體組織狀態,再冷卻時,因組織發生變化而發生變形。由於變化後的組織因冷卻方法而異,因此變形程度也因冷卻方法而異。
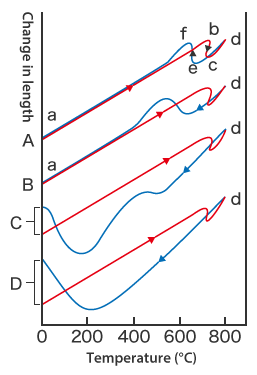
該圖顯示了不同冷卻方法的變形差異。
例如,在A(爐冷)的情況下,加熱時會發生熱膨脹(a→b),加熱時在750℃左右(b→c),冷卻時在730℃左右(e→f)會出現相變引起的尺寸變化。
此外,C(油冷)和 D(水冷)在冷卻後出現明顯的長度變化。
- A:爐冷(徐冷)
- 這是一種即使在加熱後也不從爐中取出而在爐中冷卻的方法。以每小時約 30°C 的速度冷卻。相變後成為珍珠岩組織。
- B:風冷
- 加熱後,將其從爐中取出並在室溫下冷卻。相變後變成索氏體組織。
- C:油冷
- 這是一種加熱後用油冷卻的方法。通常用約 60°C 至 80°C 的油冷卻。相變後,部分奧氏體變成屈氏體組織。
- D:水冷
- 用約 40°C的水冷卻。相變後變成馬氏體組織。
熱處理變形問題的對策
除了上述的相變問題外,熱處理引起的相變問題的原因還包括表面形狀、加熱和冷卻等方面的缺陷和不均勻性等。本節描述這些現象、的原因和對策。
淬火裂紋
這是材料開裂的一種現象。淬火後,冷卻至約200℃以下時,或淬火後次日等時候也可能發生。

- 原因:
- 可能是因加熱和冷卻不均勻引起的體積膨脹造成的形狀不良,淬火後立即回火不充分,以及淬火溫度過高等原因所致。
- 對策:
-
- 重新考慮產品的形狀和表面狀態。
- 淬火後不要冷卻到 約200°C 以下。
- 淬火後立即回火。
- 降低淬火溫度。
磨削裂紋
這是鋼材在熱處理後進行磨削加工時材料開裂的現象。又稱“研磨裂紋”。磨削裂紋有兩種類型:“第1種磨削裂紋”是在切削、研磨等加工過程中表面溫度上升到100℃左右時發生的,而表面溫度上升到300℃左右時發生的稱為“第2種磨削裂紋”。
-
第1種磨削裂紋
-
第2種磨削裂紋
- 原因:
- 當殘留奧氏體相變為馬氏體時,會膨脹。這種膨脹引起的應力會導致開裂。在切割和研磨等加工過程中,當表面溫度被加熱到約 650°C 至 850°C 時,也會發生這種情況。
- 對策:
-
- 進行適當的回火。
- 抑制因磨損摩擦而產生的熱量。
淬火變形
熱處理引起的鋼材變形,有因淬火、回火時熱脹冷縮引起的“熱變形”和因組織變化引起的“相變體積變化”。
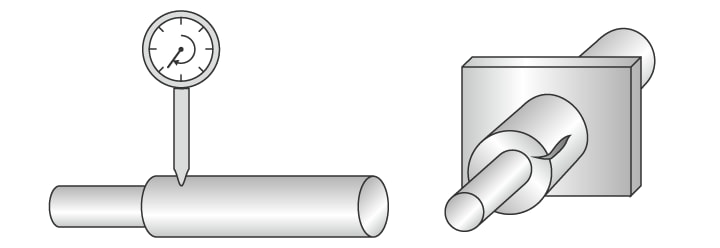
- 原因:
- 這是由於加熱/冷卻不均勻,快速加熱,快速冷卻和局部厚度不均勻引起的。在形狀複雜的情況下,是零件內部溫度不均勻等原因造成的。
- 對策:
-
- 檢查形狀,以便可以進行均勻的加熱和冷卻處理。
- 降低加熱/冷卻速率。
以往熱處理後變形量測的問題
檢查熱處理後的尺寸和形狀是否在公差範圍內是非常重要的。特別是對於形狀複雜的產品,需要高精度和定量的3D形狀量測。
迄今為止,熱處理後變形的量測都是用輪廓形狀量測儀或三維量測儀進行的。然而,在以往的三維量測儀和輪廓形狀量測儀的情況下,難以進行準確的量測,存在著偏差等各種問題
使用輪廓形狀量測儀進行變形量測的問題
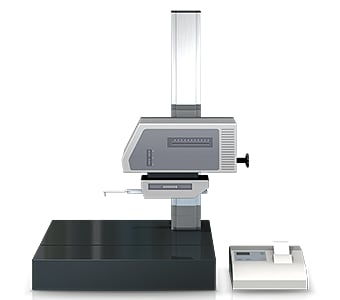
輪廓形狀量測儀是用稱為測針的觸針在對象物表面進行描摹,量測並記錄輪廓形狀的設備。近年來,也有機型使用雷射代替觸針,通過非接觸式描摹輪廓來應對複雜形狀的量測。一些機型能夠量測頂面和底面。
輪廓形狀量測儀需要為量測點取一條準確的量測線。
因此,存在以下問題。
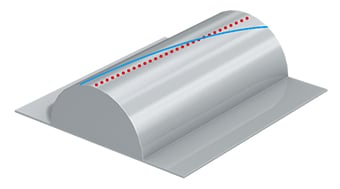
- 將樣品固定於治具並調平等作業需要時間。此外,準確找平需要與輪廓形狀量測儀相關的知識和技能。
- 輪廓形狀量測儀的觸針繞觸針臂上的支點做圓弧上下運動,觸針尖端位置也沿X方向移動,造成X軸數據誤差。
- 準確地按預期通過針的作業非常困難,即使是最輕微的針錯位也會導致量測值發生偏差。
- 很難增加 N,因為需要針對特定點進行量測。
- 由於只能獲取部分量測值,因此無法進行表面評估。
使用三維量測儀進行變形量測的問題
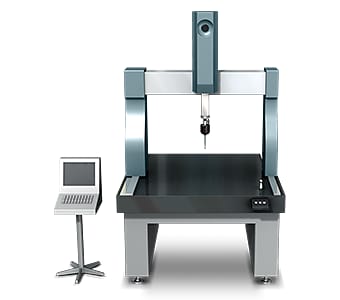
通常,三維量測儀使用一種稱為“掃描(仿形)”的方法進行量測,其中將探針應用於量測部位並進行跟踪(運行)。掃描量測以恆定間距量測多個點。
該量測方法存在以下問題。
- 將針如期穿過圓柱的中心、垂直於彎曲的線或穿過圓心的線是非常困難的。另外,在圓心角較淺的圓角R的情況下,整個圓周是由短圓弧計算的,因此微小的量測誤差會被大大放大。量測點的這種錯位也可能會導致值的細微偏差。
- 量測細小部分的 三維形狀時,可能無法使測頭接觸量測位置。此外,由於量測精度與要量測的點數和線數成正比,因此需要量測很多點。
這樣一來,在現場並不是每個人都能準確量測,還有不能量測的部位,量測儀的安裝位置還受到限制,這些就成了一個大問題。
熱處理後變形量測中的問題解決方法
以往使用的一般量測儀存在固定對象物需要時間,立體對象物和量測點是在點和線接觸時量測的問題。為了解決這些量測問題,KEYENCE 開發了表面 3D輪廓量測儀“VR 系列”。
可以以非接觸方式準確捕捉對象物的 3D 形狀。此外,可以在最快 1 秒內對量測台上的對象物進行 3D 掃描,以高精度量測 三維形狀。因此,可以在量測結果沒有偏差的情況下瞬時進行定量量測。這裡就其具體的優點進行介紹。
優點一:最快1秒內即可完成多點量測
“VR系列”可以以最快1秒的單次速度量測平面上對象物的3D形狀(80萬個數據),大大縮短了迄今為止多點量測所需的時間。可以即時準確地量測對象物整個表面的最大和最小凹凸,並可在預先設定的公差範圍內快速評估對象物的所有部位。
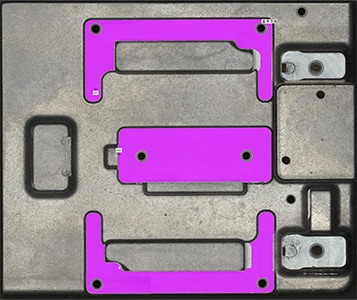
此外,一旦工件被掃描,就可以量測與先前量測時不同部位的輪廓(橫截面形狀)。無需再次特意準備同一個體並再次量測。
優點二:能夠對比參考數據和量測數據
“VR系列”不僅僅限於能夠高效地收集數據。量測數據當然可以進行列表顯示,並且可以一次對所有數據應用相同的分析內容。
例如,可以量測多個對象物的形狀,一目了然地檢查熱處理前後數據的差異,以及NG品與標準品的差異。這使得定量分析和評估熱處理引起的變形變得容易。
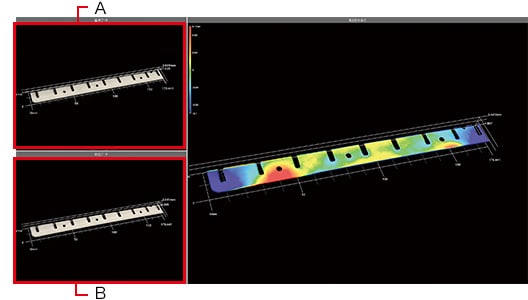
- A
- 參考數據
- B
- 量測數據
此外,可以快速量測以前需要花費大量時間和精力的複雜形狀的對象物。由於所有的量測結果都轉化為數據,可以大大減少後期數據比較和分析作業所需的時間和精力。
總結:顯著改進難以量測的熱處理後的變形,提高量測效率
使用“VR 系列”,可以快速量測和量化熱處理過程中的形狀變化,這在以往由於量測耗時而使得N點受到限制,或者由於形狀複雜而無法量測。這使得在更高水平和更有效地實現品質評估成為可能。
- 由於在平面上進行量測,因此可以同時獲取多點數據。可以大大縮短複雜形狀的量測時間。
- 可以在列表中比較多個量測數據,並且可以了解和分析由於各種熱處理引起的變形差異。
- 消除因人而異的量測值偏差,實現定量量測。
- 操作簡單,無需定位,只需將對象物放在量測台上,按下按鈕即可。消除對個人量測作業的依賴。
- 由於可以輕鬆、高速、高精度地量測 3D 形狀,因此可以在短時間內量測許多對象物,這有助於提高品質。
此外,與過去的3D形狀數據的比較、粗糙度分佈等可以輕鬆進行分析,因此可以用於各種用途,例如根據溫度對斷口狀態進行趨勢分析和破壞狀態的確認。