精確測量截斷後底切形狀

衝壓加工包括截斷、彎曲、擰轉等多種加工方法。其中,還有衝孔、開槽等加工方式,是採用「裁斷」方式的力量。透過截斷形成的面稱為裁斷面,透過觀察該面的形狀,可以了解衝床和模具之間的間隙(間隙)的狀態。
因此,在本節中,我們將針對截斷加工的基本知識和底切的產生原理進行說明。此外,我們將介紹包括底切、截斷面測量問題和解決方案。
何謂底切
底切是一種發生在截斷產品表面的現象。這是材料被衝床和模具切割時,材料被切割表面產生的拉力拉扯,導致表面光滑的現象。的大小和形狀,會依照衝床和模具之間的間隙(間隙)而變化。衝床和模具之間的間隙,莫大影響了產品的品質和壓力機的使用壽命。
截斷加工的截斷面
截斷加工的切割面具有底切、截斷面、斷裂面、毛刺4層結構,即使是平面板狀也不會變得光滑。
首先,如前所述,「底切」是透過拉動加工材料的表面,所產生的光滑表面。「截斷面」是透過穿透加工材料的衝床,所形成的光亮表面。由於衝床和焊接金屬與加工材料的摩擦造成的傷痕,截斷面有細小的垂直條紋。「斷裂面」是比截斷面更粗糙的表面,給人一種加工材料被撕裂的感覺。然而,「毛刺」具有堅硬、鋒利的形狀,並且呈鋸齒狀。
這些切割面的狀態會依照加工材料、衝床下降速度、衝床和模具之間的間隙大小,以及其他因素而變化。

- A
- 底切
- B
- 截斷面
- C
- 斷裂面
- D
- 毛刺
- E
- 板材厚度
何謂間隙
「間隙」是衝床和模具之間的間隙,切割面的狀態依照間隙的數量而變化。另外,適當設定的間隙稱為「適當間隙」。
間隙量非常重要,因為會影響截斷品質(尺寸準確度、防止底切和毛刺等)和模具壽命。如果間隙正確,從衝床側和模具側產生的龜列將在中途變得一致。這種一致的情形被稱為「會合」。理想的截斷加工過程是不會產生底切或毛刺的「全面截斷」,但據說即使有適當的間隙,也很難實現。
間隙設定和切割面之間的關係,如下所示。
適當的間隙

如果間隙適當,截斷面將以板厚的1/2至1/3的比例均勻地出現在整個板上。如果間隙不固定,則截斷面的比例會出現局部差異。
間隙過大

如果間隙過大,會增加底切和毛刺,導致產品準確度不穩定。同時,由於衝壓壓力引起的翹曲(衝壓翹曲)也會增加。
間隙太小

- A
- 二次截斷
如果間隙太小,則衝床和模具的切削刀刃產生的龜裂將不一致(會合),進而因「二次截斷面」而產生鬍鬚狀毛刺。此外,衝床和模具上的荷重也很大,這將造成被稱為「磨蝕」的模具損壞原因。
合適的間隙值因加工材料和板厚而異,一般數值可透過以下公式算出。
單側的間隙 = %x加工材料的板材厚度
※「%」是間隙與板厚的比率。由於將會隨材料和衝壓準確度而異,所以透過實際的試驗值來算出。
截斷過程
截斷加工的切割過程如下:
① 將衝床壓在加工材料的上面
- 會像彎板一樣的狀態,加工材料會出現「底切」。

- A
- 衝床
- B
- 板材
- C
- 模具
- D
- 間隙
- E
- 底切
- F
- 截斷面
②無法承受彎曲時,衝床會陷入材料內部中
- 隨著衝床和模具的截斷力,將產生龜裂情形。
- 當加工材料無法再承受拉力時,就會產生龜裂情形。
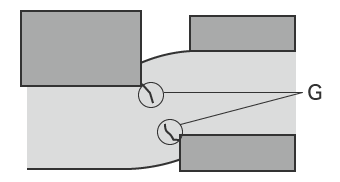
- G
- 龜裂
③透過衝床和模具的角部,讓拉伸力作用在加工材料上
- 從衝床和模具的切削刀刃上出現的龜裂擴大並貫穿(會合)時,就會產生毛刺。

- H
- 龜裂貫穿
所謂的截斷就是指當截斷力作用在加工材料上時,產生截斷面的過程。
傳統底切測量的問題
到目前為止,衝壓的底切通常被使用於 投影機、或輪廓測定機進行測量的情形。然而,想在廣泛的板材中精確測量底切,存在以下問題。
使用 投影機進行底切測量的問題

光學測量儀器的一種,測量原理與光學顯微鏡相似。透過將對象物放在載物台上並從下方照射光線,對象物的輪廓會被投射到布幕上。一些大型布幕的直徑超過1m。測量已打孔的寬平面底切時,需將其調整出水平狀態。
該測量方法存在以下問題。
- 由於 投影機只能從垂直於切割面的方向觀察才能取得剖面形狀,因此必須將對象物放置在可以看到底切部分的位置,並且必須在準確水平的狀態下進行測量。這時候就出現了對象物放置方式不固定的問題。
- 如果工件的形狀複雜,可能會產生光影,使得無法從垂直方向進行觀察。此外,由於無法取得尺寸和圖面差異的數值,因此難以保存和比較資料,並且需要將輪廓形狀轉移到描圖紙上。
這樣一來,就不僅不是現場的每個人都能準確測量,還會有無法進行測量的地方,而隨著對象物的不同,也可能需要加以切割等,這將是一個很大的問題。
使用輪廓測定機進行底切測量的問題

輪廓測定機是使用稱為尖筆的觸針,透過描摹出對象物表面,藉以測量並記錄輪廓形狀的裝置。近年來,也有的類型是使用雷射代替觸針,透過非接觸式描摹追踪輪廓來測量複雜形狀。此外, 某些型號能夠測量上下兩面。
當使用輪廓測定機測量經打孔的寬平面底切時,則需要調整出水平狀態。
該測量方法存在以下問題。


- 將對象物固定到夾具上,並調整出水平狀態需要時間。此外,具備輪廓測定機相關的知識和技能,對於準確地調整出水平狀態極為重要。
- 輪廓測定機的觸針將繞著觸針針臂上的支點做圓弧上下運動,觸針尖端也會沿著X方向移動,造成X軸資料產生誤差。
- 準確地依照預期穿針非常困難,即使是最輕微的針錯位也會導致測量值發生偏差。
底切測量中的問題解決方法
傳統所使用的一般測量儀器,存在著需要耗費時間固定目標物的問題,以及必須在點狀或現狀接觸立體目標物、測量位置,才能進行測量的課題。為了解決這些測量問題,KEYENCE開發了一次性3D形狀測量儀「VR系列」。
能以非接觸方式,準確捕捉對象物的3D形狀。此外,可以在短短1秒內對台上的對象物進行3D掃描,以高準確度測量3D形狀。因此,可以瞬時進行定量測量,而不會出現測量結果偏差的情形。以下將介紹其具體上的優點。
優點1:無需固定對象物,即可測量
無需水平固定對象物,即可進行測量。例如,即使在打孔加工中測量寬表面的底切時,也不需要加以固定。
「VR系列」可以透過非接觸的表面測量,來準確測量出底切狀態。此外,透過使用可以事先登記測量項目的分析範本,可以在短時間內執行工件形狀分析,因此現在可以在短時間內執行以前費時或不可能的測量。

優點2:無需複雜設定的「自動對齊功能」
無需水平固定對象物,即可使用自動對齊功能對齊對象物。
「VR系列」自動高準確地對齊3次元位置。您可以透過添加傾斜度、基準面和高度偏差等各種因素輕鬆進行微調。還具有允許您在檢查影片時,指定測量點的功能。可以在確認放大觀察圖片的同時,使用幾何工具指定測量點,因此不會出現因操作者的熟練程度而有所不同的情形。

優點3:最快1秒測量出整個「表面」的形狀

測量演算法和硬體已經完全改善,以實現最快1秒的測量速度。瞬間掃描完畢整個面的資訊。目標點也可以自由測量。不同人進行測量,測量數值也不會出現差異。
「VR系列」以最快1秒的壓倒性速度,實現了N的大幅增加並縮短作業時間。這將提昇測量品質,將檢驗人員的人手調動成生產人員,進而促進增加產量。無論是評估試做品還是出貨前的產品檢查,速度將能改善任何測量任務。
總結:顯著改善難以測量的底切形狀測量效率
使用「VR系列」,高速3D掃描可以在不接觸的情況下,即時測量對象物的準確3D形狀。可以解決一般測量儀器的所有問題,如底切、截斷面、斷裂面和毛邊等。
- 無需切割對象物,即可測量剖面。
- 消除因人而異的測量值差異,實現定量測量。
- 操作簡單,無需定位,只需將對象物放在載物台上,按下按鈕即可。消除對個人測量工作的依賴。
- 由於可以輕鬆、高速、高準確度地測量3D形狀,因此可以在短時間內測量許多對象物,能有助於提升品質。
此外,與過去的3D形狀資料和CAD資料進行比較,可以很容易地分析公差範圍內的分佈,因此可以用於產品開發和製造趨勢分析、抽樣檢查等各種目的。